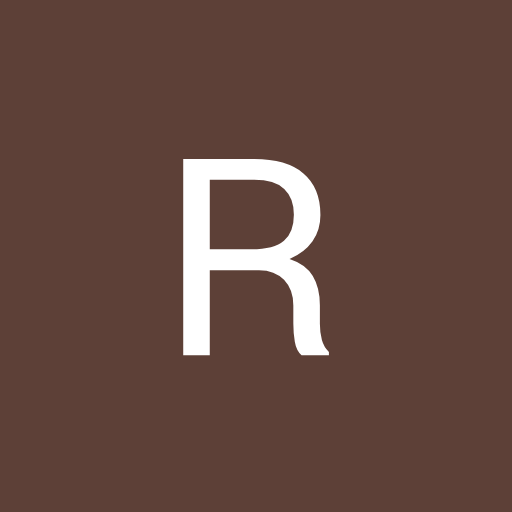
rationaltechnician
Forum Replies Created
-
The 34-6 error while unit is off is an unrelated problem the RESET GAS and likely the switch on PCB, one leg opening and other staying closed. Check this and update us.
-
I see Service 11 as the subject line so I will go with that.
This error means when the steam generator is filling, it measured more water than steam generator can hold until the water level probe sensed the water.
In most cases, this means water is passing the venting valve at the same time steam generator is filling.
It can also mean intermittent water level sensing if you got a little bit of scale forming on the water level electrode.
As a more complex problem, it could mean either the reference volume of steam generator is incorrect or the CDS is not set for 1000 pulses/litre. This is less likely.
-
I'm sure you got your answer by now but for the benefit of others seeing your post, I will try to offer some information.
Service 52 was introduced with Index I (2016-09) units which now have LED lights in the door. The possible reasons by RATIONAL is to check the cable from A7 to A8. The A7 board is usually mounted near the top right hand when you are looking at the left side service access. The A8 is a board that was mounted inside the door. However, in later models this was replaced with a new harness that eliminates the A8 board for a more waterproof design.
If you have the A8 board, this can be retrofitted but you need to provide a serial number.
Besides the A8 board, the fault is usually at the door hinge. The LED harness runs through the door hinge and can be damaged if the door trip tray (table models) or hinge cover (floor models) is knocked out and it is now exposed. Pinching of this wire can now occur.
On stacked units, the top unit LED harness can get damaged as the operator removes and reinstalls the metal drip pan.
If this error is combined with a Service 34.X, you should also inspect the interior halogen bulb and socket. A short here goes back to the A7 board and can create either of the errors.
Check also for connections on the LED bars. Many operators keep the door open slightly which now allows heat from the interior cabinet to reach the LED's. Doing this is not a good idea even before the LED's were introduced. Either door should be closed or open completely to avoid unnecessary repairs. This can also cause the LED optics to become brittle and crack over time.
Hope this helps!
-
Hey Sanket
Have you already found this problem?
When diagnosing a leak, determine if the water is clear, translucent or dark brown.
Clear water could be like you said steam hose. On a 61E, it is hard to see because it is concealed behind steam generator. Use a dry paper towel and hold it there while unit is in steam mode. In fact, do this at all hose clamps while activating solenoids in function test for at least 1 minute each.
White or translucent water suggest it would be happening during cleanjet. You need to check motor shaft gasket and also meat probe connections. These leaks actually happen behind the cabinet insulation and won't be detected until it finally drips under the unit.
Greasy water can also be during cleanjet. Check suction and pressure hose from cleanjet pump but also the pipe between door drip tray and drain valve. You may need to remove the hand shower cover plate and make sure this is assembled correctly still. Overtime grease builds up around this and won't stay aligned. Clean it immaculately to correct this problem.
I assume you already checked;
Door gasket Hand shower hose reel connections moisture nozzle on element (pipe through element flange) rack pins unit level drain connection (no 90 or p-trap close to unit) quench nozzle not worn and spraying through emergency overflow.Either case, let us know what you found, we can let you know about any repair kits if applicable.
-
rationaltechnician
MemberJuly 16, 2020 at 2:24 pm in reply to: Rational service code 10 (SCC) and E13 (CM)Awesome explanation ectofix!
We also see Service 10 as one of the most common displayed errors of our customers.
Every customer uses the unit differently. Those who use the unit in continuous mode steam all day will see scale build-up because the sc-automotic ectofix described (every 2 hours on units after 2008-09, every hour units prior), will never be allowed to energize. This is because Rational does not want to disturb customers cooking. Unit door must be left open for a whole minute in this case before unit will attempt sc-automatic.
The Care tabs have a dual purpose of descaling steam generator and rinse cycle for interior cabinet.
Cleaning is critical also to prevent corrosion of the cabinet due to salts from foods and pitting by steam/chlorides in water. The stainless steel of the cabinet needs to be cleaned and dried to allow the chromium (passive) to reform.
<font face=”inherit”>Because of all these benefits, Rational recommends cleaning daily even if used in steam all day and the unit looks clean. My recommendation to our customers is clean daily after cooking in the smallest of clean cycles to save on chemicals (light or save program). This is especially for customers that do nothing but steam all day and skip cleaning because it still looks clean. For those customers doing high temp grilling/roasting will clean any way and use a higher level of </font>cleaning<font face=”inherit”> (medium or strong) because of grease and smoke. Those that don't? Well, I've seen fires starting when they open the door and the fan wheel stops spinning. In this case, the door must be closed immediately, unit switched off and allow fire to die down.</font>
-
Thanks so much, we’ll check that out.
-
rationaltechnician
MemberJune 21, 2021 at 3:57 pm in reply to: Rational SCC WE 202G heat exchanger failures as well as several other component within 1st 3 yearsYou will get an updated version of the heat exchanger.
You'll also get a USB stick to update gas settings to improve performance and reduce delayed ignition. be sure to update these and perform a flue gas analysis to optimize the burner.
-
BTW, congrats on all those Rational units. It appears the Chefs are sold on the value of these units and how it reduced the labour and improved food quality. Very soon, every kitchen in the Americas will have a Rational or another combo oven as a standard piece of cooking equipment much like in many European countries.
Us as technicians would rather be working on them when compared to fryers.
There are rumours they will also introduce the VarioCooking Centre (VCC) soon as well. There will be a new learning curve for us but a few common components with the SCC units.
-
For a tech who has never attended a Rational training, you have really grasped a lot. More than many trained techs.
From my memory, since CareControl once an index G, H or I unit detects more than 20% of steam generator volume as scale (difference of last fill to size of steam generator), the display locks out customer for 2 minutes with a Calchek message.
After the 2 minutes lapse and the unit goes back to the standard screen, you can select the oven symbol, wrench and screw driver and then a descale button should be available. If not, try opening door.
If it is still not there, it may be in the technician level after entering a password. I will check this again next time I come across a unit requesting descale.
That being said, because of CareControl, these units should never ask to be descaled because daily use of Care tabs would prevent the formation of scale from reaching that point.
This of course depends on customer cleaning behaviour and if Care tabs are actually used.
I’ll follow-up on this thread once I can confirm a few details.
-
Thanks