A sponsored post courtesy from Welbilt KitchenCare
Jay Maiden
Director of Service – Kolpak/Harford/RDI
Now more than ever operators must stay on their toes daily to keep their business running smoothly. They plan for everything from flatware, to seating, to kitchen equipment, and beyond. With a full plate, we understand there can be an attractiveness to focusing less on equipment operation and more on your customer facing needs.Â
Across Welbilt brands, our Technical Support teams stay focused on helping operators maximize their equipment operation. While they are in the field working with customers this technical team has witnessed many scenarios where even the best of intentions can be detrimental to the equipment and even to the business’ profit.Â
Our team understands that all circumstances are different, and every business must be able to improvise with each challenge they face. Perhaps some of the tips we have learned from the field can be helpful for otheroperators and servicers.
Condenser Coil – To Cover or Not to Cover??
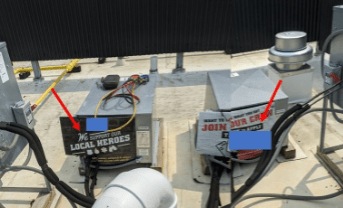
While in the field recently, our team came across a customer that had a service company cover their condenser coils during cold weather to keep their head pressure high enough for the compressor to run. However, once the weather started heating up, they forgot to remove these coverings.Â
Â
In low ambient temperatures, mainly below freezing, the head pressure may not be high enough to allow the compressor to run. Covering the condenser coil is a tool that service technicians can use to raise the head pressure. It is not done in above freezing ambient temperatures. Condensing units have a low-pressure switch that prevents the compressor from running if the operating pressure does not reach a certain pressure level. In low temperature conditions, it is difficult for the compressor to start because the pressure inside the condensing unit drops.Â
Â
Covering the condenser coil essentially raises the head pressure that enables the compressor to run. Once the
compressor is running correctly, the condenser coil should be uncovered. Compressors are designed to operate at an optimum pressure, pushing outside the design levels for an extended period can cause component failure. An average compressor failure can range between $1,500 and $2,500 to replace.Â
Maximize Your Space, But Don’t Jam Pack Your Space
Kolpak received a Warranty call with concerns that a freezer door would not shut. Upon arrival the team learned that product was stocked two days per week, and one stock supply had just been delivered. The refrigeration layout was designed that to get to the freezer, you have to walk-through the cooler first. Â
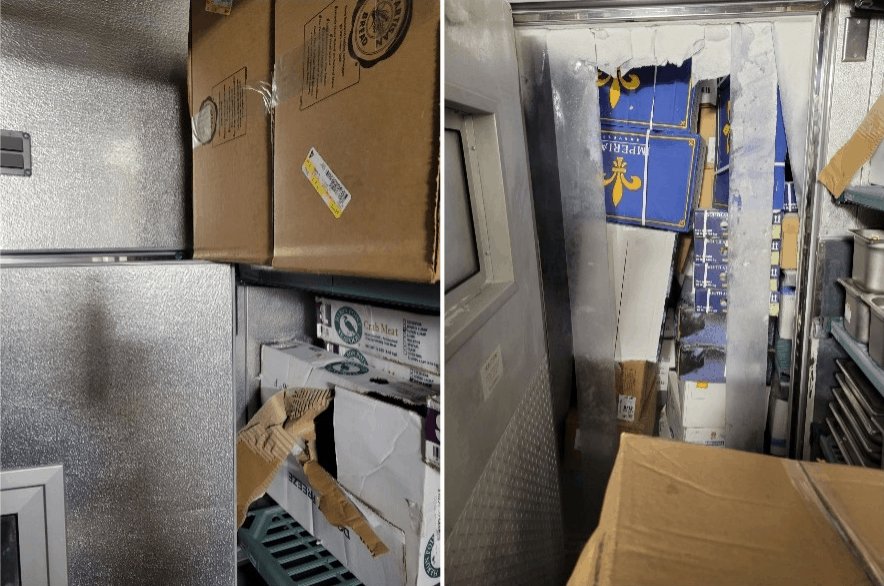
Upon inspection it was determined the cooler had so much product in it, the freezer door would not shut. We found the freezer door stuck partially open due to a large cardboard box above the door arc opening. Doors should always be free from obstructions that prevent the door from closing completely. There is too much product in the walk-in. Ideally, we would suggest less product and more frequent deliveries to minimize how much product is stored in the walk-in.
Doors not closing properly can cause frozen food to spoil and depending on the size of the walk-in and amount of food stored in it, dollar amounts can easily be in the tens of thousands of dollars in waste.
Habits – Simple Changes, Big Impact
With understandably so many variables that can play into day-to-day operation, each business must find ways to maximize their revenue. The goal of our Welbilt team is to find small changes that can make a big difference in
their Welbilt equipment operation.
Â
We have a full Self Help Library available on our website https://www.wbtkitchencare.com/Self-Help.  Our Technical Support team provides a list of FAQ, Documents, Downloads and more.