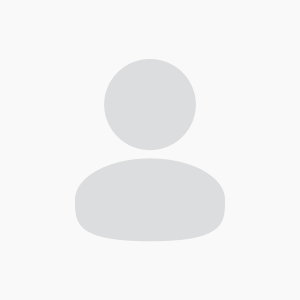
ryantruck9
Forum Replies Created
-
Greetings Carmine,
your 202G also has 2 hot air burners
if either burner fails to ignite or fails to prove ignition you will get a reset gas error.
Even if you are in steam mode the hot air burners may come on to achieve 212F
If in combi mode the hot air burners will definitely be needed.
Function test your hot air burners to see microamp readings
to help narrow down the fault check the gas error log at the end of the diagnostic menu
-
place you clamp on around the 0.8A fuse wire and function test SC Pump see what it draws and listen for scale/debris hitting pump when running.
same thing for Care pump and valve
seems like when both are running towards the end of the care control portion of cleanjet you pop your fuse.
maybe a build up of chemical in the care drawer or someone put a blue rinse puck in there
-
Hi Jeff
You don't need Rational's puller but you will need some sort of puller and a blow torch.
The tapered motor shaft seems to really bite on the fan hub so once you have removed the 13mm bolt and set up your puller with some good tension you need to heat the fan hub.
It will make an ear piercing pop when the hub frees from the shaft.
I recommend Posi Lock 106 or the HP-2 Puller kit
Stay safe!
-
Wait… you get an email on your outstanding back orders from Parts Town?
I miss the days of great customer service from Parts Town.
I have no idea what is on back order until I see a random invoice and a day or 2 later a box shows up unless I scroll
through all of my online orders looking for one that still says processing.
When they purchased heritage they shipped the Canadian parts orders to the former Heritage Canada folks.
Thereby sticking me with the same customer service experience I had gotten away from when I started using PTown originally.. gee thanks
It is unacceptable that Hobart can have 200 day lead time on a dishwasher part. Its far too critical piece of equipment for that sort of down time.
There is a place in the US that repairs OEM factory controllers. (you send it in they recondition it)
Fixbear I believe posted the company name on here a few years ago
Hobart has emptied most Canadian warehouses so there is never a part in town or “up north”
I think they consider freight charges an untapped income source. End user has to pay whatever the freight charge is and it isn't regulated like list price of the part itself.
>end of rant<
Have a good weekend be safe out there
-
the unit must be front flueing to melt that high temp wire.
I think your gas valve opens to 1.3″WC then ramps up to
3.5″WC.
Leave your manometer on the manifold for the entire heat/pressure up and ensure no gas pressure “creep” or hunting
replace the ignitor /housing (S44096) with a new wire (44169) and the front baffle plate (S44135) insulation. It is likely in poor shape from all the service over the years
poor condition front baffle could allow front flueing
Sometimes the flue riser can “bow in” decreasing flow.
If the unit is level, the front plate and box are new (fairly sealed) operating at the correct gas pressure with clear tubes and an flue it should not front flue.
-
-
that looks to be a Garland H280 series
H286RC if it has a convection oven. drop the RC if no C/oven
the salamander looks like a GIR36
-
Hi Addenlamb
If you stand in front of the unit can you lift the Ultra Vent by simply pushing the exhaust canopy up?
If so it may not have been installed correctly or some hardware has gone missing.
there should be a nut holding the hood to the Combi
one of the 3 bolts on the door hinge bracket should have been removed at installation and a 2 sided
stud threaded in. assuming you have a left hinged door
If not this check the drain hose on the Ultra Vent to make sure it isnt plugged or routed poorly to an open drain
-
I have a couple questions:
Is this a 120V unit?
By power transformer are you referring to a round step up transformer?
Â
this round transformer powers all the 240V parts. (pumps and valves)
It should have 0.8 Amp fuse protecting the transformer secondary (240VAC)
make sure this fuse hasn't been replaced with a higher current rated fuse.
As i am sure you are aware the fuse is quite a bit cheaper than the transformer
Â
You likely have a leak that is causing a short at your clean jet pump.
check your clean jet pump and mounting box for debris or water/sludge indicating a leak
if it is a large leak you may have dried up detergent covering the floor of the control area
the leak HAS to be repaired before replacing the pump or it will short again
Â
It could also be a solenoid valve that has shorted (Y2 quench, Y3 moistening perhaps)
i am not sure of your S# or age of unit, they use different valves for cleaning depending on age
-
As ectofix has mentioned it could be any of the 230V components.
Function test all your pumps and valves.
if nothing blows your .8A fuse it may be a leak causing a short.
Check the cleanjet pump for moisture or see if there is any residue under the pump.
if you have a small leak during cleaning it may take awhile for the water/grease/chemical solution to make its way to the cleanjet pump/ box
It is usually dry by the time a tech comes to troubleshoot but you may see gunk on or under the pump
Do the same for the care control pump as it probably had not been activated in the 30 min you were watching the unit
function test Y3 moistening valve for a solid 90 seconds
the hose clamp to the cavity nozzle has been a leak point and often it takes a bit of time for the leak to develop as pressure needs to build up before it starts to drip.
Your machine fills the quench box with Y3 during cleanjet
it takes a while with the small cavity orifice so you really need to function test it for well over 1 min
(previous generations filled with Y2)
good luck and stay safe!